23
Feb
BUSBAR TRUNKING SYSTEM For Electrical Power Distribution
BUSBAR TRUNKING SYSTEM
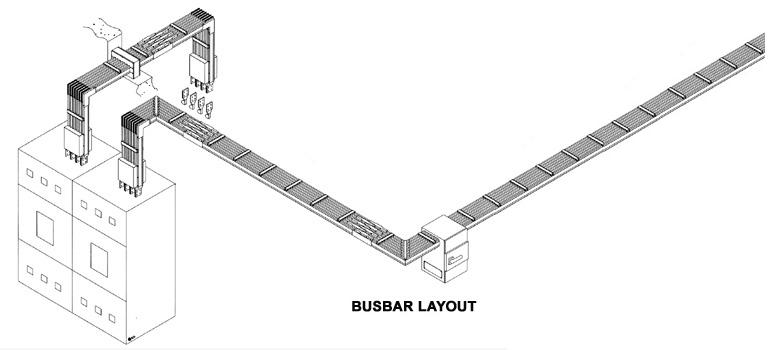
BUSBAR TRUNKING SYSTEM involves the distribution of electrical power using a set of copper/Aluminum bus bars enclosed in a suitable encloser with a high degree of protection against any ingress of foreign bodies.
Following are some advantages of Bus bar trunking system over normal cabling system:-
- On-site installation times are reduced compared to hard-wired systems, thus leading to cost savings.
- It provides increased flexibility in design and versatility with regard to future modifications.
- Greater safety and peace of mind for specifiers, contractors and end-users.
- Because of the simplicity of busbar, it is easy to estimate costs from the design/estimating stage through to installation on site. This is because the technical characteristics and price of each component are always known.
- It is short sighted to compare the cost of busbar against that of a length of cable — and not the real cost of a cable installation to include multiple runs of cable, tray and fixing, let alone the protracted time and effort of pulling cables.
- Distribution busbar distributes power along its length through tap-off points along the busbar at typically at 0.5 or 1 m centers. Tap-off units are plugged in along the length of the busbar to supply a load; this could be a sub distribution board or, in a factory, to individual machines. Tap-offs can normally be added or removed with busbar live, eliminating production down time.
- Installed vertically the same systems can be used for rising-mains applications, with tap-offs feeding individual floors. Certified fire barriers are available at points where the busbar passes through a floor slab. Protection devices such as fuses, switchfuses or circuit breakers are located along the busbar run, reducing the need for large distribution boards and the large quantities of distribution cables running to and from installed equipment.
- Very compact so provides space savings
- Where aesthetics have to be considered, busbar trunking can be installed with natural galvanized, aluminum, or painted finish. Special colors to match switchboards or a specific color scheme are also available on request.
- Busbar trunking has several key advantages over conventional forms of power distribution including: –
(a) Reduced, on site installation times when compared to hard-wired systems thus leading to cost savings.
(b) Increased flexibility in design and versatility with regard to future modifications.
(c) Increased safety features brought about by the use of high quality, manufactured components, which provide greater safety and peace of mind for specifiers, contractors and end-users. - Uneven distribution of current takes place where multiple runs of cables are used in parallel.
- Busbar trunking has tap-off points at regular intervals along each length to allow power to be taken off and distributed to where it is needed. Because it is fully self-contained it needs only to be mechanically mounted and electrically connected to be operational.
- For higher ratings of power distribution we need to have multiple runs of cable. In such conditions unbalanced distribution of current takes place and causing overheating of some cable. This is completely avoided in the BTS systems.
- When multiple runs of cables are used it often leads to improper end connections thereby causing overheating of contacts, burning of cables ends, and is a major cause of fire. This is completely avoided in BTS systems.
Busbar versus Cables for Riser Applications:
Sr.no |
Issue |
Cable |
BUSBAR |
1 | Number of circuits | One circuit per floor. Hence for a 20-floor building, you need 20 circuits. | Just one circuit can cover all floors. |
2 | Main Switchboard | Need 1 outgoing for each circuit. Hence 20 nos. MCCB outgoings. Higher cost and larger space requirement in electrical room | Need only 1 outgoing for each riser. Lower cost and size of main panel. |
3 | Shaft Size | Using 4 core cables, and considering 1 cable per feeder, you need 20 cables on the lowest floor. Large space required for cables/ cable tray. | Typical size of 1600A riser is 185mm x 180mm. Leads to big savings on riser shaft size, and hence more usable floor area on every floor. |
4 | Fire & safety | The high concentration of insulating materials used in cables and conductors involves a very high level of combustive energy. | The volume of insulating materials used in trunking is reduced to a minimum so combustive energy is considerably lower than cables. The insulating materials used do not release corrosive or toxic gases in the event of a fire. Once the source of the fire is removed, these materials are extinguished in a few seconds so that the effect of the fire is minimised. |
5 | Combustive Energy – see table enclosed | 1600A – approx 60 kWh/sq.m | 1600A – approx 5 kWh/sq.m.
Combustive energy is typically 80% –90% less than cables. |
6 | Future expansion | If load on any floor exceeds initial plan, owner has to run an additional cable from a spare feeder on main board to that floor. | By providing extra tap off slots on each floor at the design stage, owner only has to procure a tap off box and plug it in wherever additional load is required. As the plug in can be done live, there is no shut down required for any of the existing clients / circuits. Future Flexibility. |
7 | Fault withstand levels | Limited by conductor size of each circuit. | Much higher – typically a 1600 A riser has a fault withstand capability of 60 to 70 kA. Safer in an electrical fault. |
8 | Installation time | Much longer | Each riser on a 20-floor building can be installed in approximately 2 to 3 days. |
9 | Voltage drop | High impedance if you choose cable size based on each floor current rating. | Much lower impedance. Hence substantially lower voltage drop. |
Learn more about Busbar Trunking: Advantages Over Cable
Latest posts by ESDS (see all)
- Small Business Website: Building a Strong Online Presence - March 11, 2025
- Top 10 Best Practices for Implementing DRaaS in 2025 - January 20, 2025
- Signs of Cyber Attack and How to Respond to them? - March 25, 2019
Dear Sir/Madam, I liked your information about rising main but we need some comparison with FACTORY AREA having 280 machine and haveing 4 trasnformer connection its spinning mill . Please give more detail about your company have bussiness in common.
Regards
Albert John
For busbar trunking system is really critical preliminary engineering work.
I want know BBT.
Sir,
Thank you very much to the information you have given, a knowlege that I will treasure,please i would like to request a simple design how big is the bus bar if I put a certain power from supply side to load side
Thaank you very much
Noel Ruiz
I am a electrical design enginner currenly involved with electrical system design of an international airport. I need information of a LV enclosed bus bar trunking system to coonect LV side of a 11kV/400V 1250 kVA transfor and 2000A, 400V ACB. Would you please mail me its detail and price per meter of such system.
Good general knowledge. We can use in setting up of our new plant especially from safety viewpoint and ease of maintainence. Thank you for summarizing so aptly.
BUSBAR TRUNKING RATE OF CUPPER BAR
Those points are really impressive for following. Just a quick note to tell you that I have a passion for the topic "Electrical Power Distribution" at hand. Thanks for this discussion.